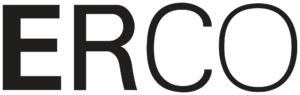
Optimization of capacity and shift planning of employees
In cooperation with mindsquare, it was possible to establish a more efficient manpower and shift planning for ERCO GmbH which significantly simplifies the planning process.
The medium-sized company ERCO based in Lüdenscheid is positioning itself in the lighting industry with a specialization in architectural lighting with LED technology. The company is responsible for the lighting of international buildings for example the Brandenburg Gate or the Louvre in Paris.
The initial position
The employees of ERCO used their own system to create the shift planning of the employees. Furthermore, the existing capacities were entered in a separate tool.
However, it has become increasingly clear that summarizing the capacity and shift planning of employees within a tool would make cycles much more efficient and avoid duplication of care, standardize the planning process and optimize capacity planning as well.
The implementation
As part of a workshop, the current processes were recorded, the requirements of the company developed and the target image for workforce management was established. It should be a Fiori solution which goes beyond meeting the requirements with intuitive use and modern interfaces.
During the course of the project, mindsquare acted directly on site as well as remotely in close cooperation and consultation with ERCO. An initial challenge was the patch state of the in-house gateway system, where workarounds had to be worked on to develop the application directly on the ERCO system. After a system upgrade, this hurdle was overcome. In addition, the performance of the system has been further improved despite the high volumes of data required in workforce scheduling.
During the project implementation phase, the entire team pulled together. In particular, the communication of the project participants worked well. With short communication channels and through the constant exchange with each other, goal-oriented decisions could be made quickly and solutions could be found. The project management on ERCO’s side also served as a mouthpiece between mindsquare and the users, so that emerging requirements could be dealt with quickly.
The project result
ERCO now uses optimized workforce planning with a modern and intuitive Fiori-based interface. This is tailored to the needs of the planners as well as to the requirements of the overall MES project.
Now, the users can schedule the staff throughout the entire production process depending on the utilization of the current order situation. This also takes into account the observance of rest periods. If there is a shortage at your workplace, available employees can be borrowed from other workplaces.
The qualifications of the employees and the actual degree of utilization of the workplaces are also used to calculate the capacity provided. As a result, the system calculates the number of hours spent on the order on each day. Finally, there is the accelerated shift planning, where the responsible employees are notified of any problems in the planning.
Over the course of the project some hurdles were taken together. One of these hurdles was the acceptance of the end users due to the insufficient performance during the test phase. In particular, ERCO praised the efforts on the part of mindsquare to remedy any complications. In addition, the high availability and responsiveness of the team as well as the regular attendance at ERCO were highlighted.